Take a Look inside Cartier’s Maison des Métiers d’Art
For a look at Cartier’s commitment to artisanal crafts, just look at its Maison des Métiers d’Art and the techniques it has pioneered
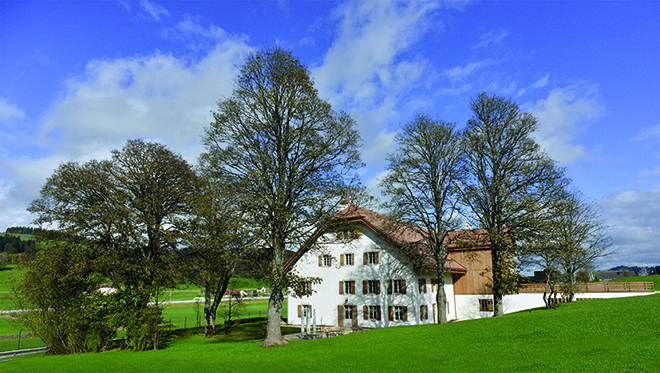
Cartier’s Maison des Métiers d’Art in La Chaux-de-Fond, which is established in a converted farmhouse dating back to the late 18th century
Metiers d’art watches demand specific savoir faire such as guillochage or micro-painting, which often fall outside the usual purview of watchmaking. To produce such watches, some brands choose to partner with external craftspeople, who provide the expertise necessary to bring a particular design to fruition. It’s an elegant (and convenient) solution, because these watches tend to have limited runs anyway, so the brand is free to pursue new projects once its current ones end.
Cartier, on the other hand, decided to bring these savoir faire under its roof – literally – when it established its Maison des Métiers d’Art in La Chaux-de-Fond. Such integration echoes its efforts elsewhere within the manufacture, which now boasts six facilities across Switzerland with capabilities such as vintage clock and watch restoration, hand production, and the manufacture of watch crystals with exotic shapes. Consolidating a range of metiers into a single space doesn’t just allow a brand to reap the typical advantages of having “in-house” expertise, like shorter product development cycles. As Cartier has shown, when such know-how reaches a critical mass, it becomes possible to push the boundaries and either create new artisanal techniques and crafts, or adapt existing ones specifically to the context of watches.
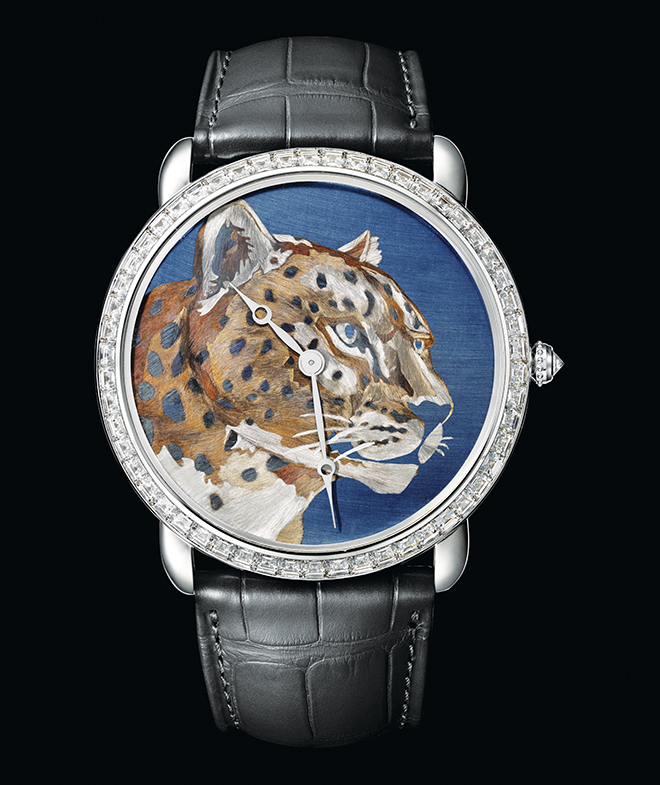
Take a Look inside Cartier’s Maison des Métiers d’Art , introducing the Ronde Louis Cartier XL Flamed Gold watch
Painting with fire: Take a Look inside Cartier’s Maison des Métiers d’Art
The latest metiers d’art technique that Cartier has developed is flamed gold, which combines elements of engraving and heat treatment. These are applied to an 18K white gold alloy that Cartier developed with its external supplier; the alloy’s unusually high iron content allows its surface to oxidise and take on different colours when heated to different temperatures, much like how steel watch hands are blued by heating.
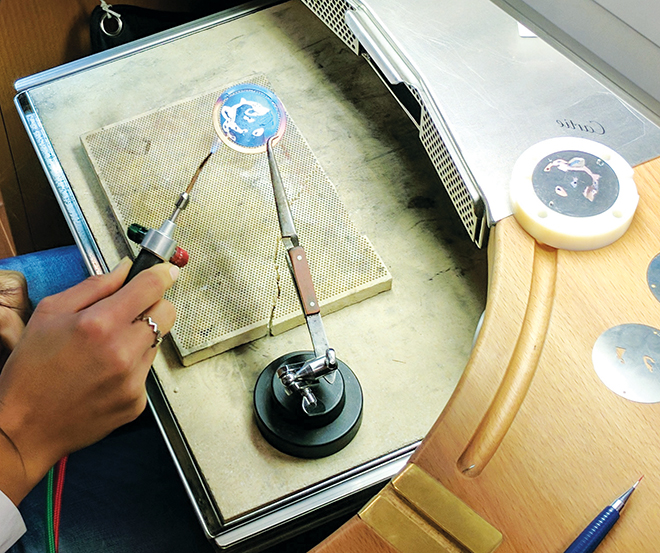
Take a Look inside Cartier’s Maison des Métiers d’Art, here, the white gold dial of an unassembled Ronde Louis Cartier XL Flamed Gold watch being fired with a blowtorch
To create the panther motif seen on the dial of the Ronde Louis Cartier XL Flamed Gold watch, the Maison des Métiers d’Artisan first heats the entire dial to the highest permissible temperature with a blowtorch to create an evenly blue canvas. The portions of the dial that are supposed to take on a different colour are then scratched with a ceramic tool to remove the oxidised surface and expose the original white gold dial underneath. The blue portions are masked off before heat is applied again, but to a lower temperature this time to create a different colour. The various shades of beige and brown are achieved sequentially on the dial, in a process that requires five separate applications of heat. Besides removing “unwanted” colours off sections of the dial, scratching is also responsible for creating the nuanced textures on the panther – note how the panther’s sclera, for example, has been engraved with lines that radiate outwards from its iris.
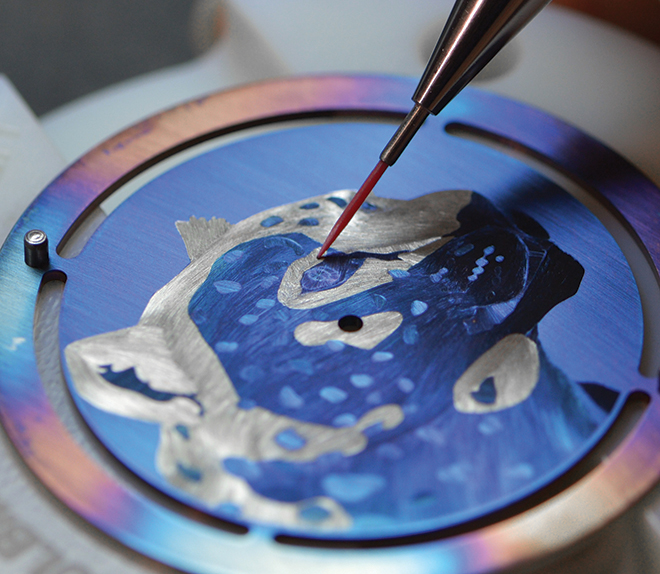
The unwanted portions of the dial that have been blued are scratched with a ceramic tool to reveal the unaltered surface underneath
Each flame gold dial takes an artisan nearly 50 hours to complete, and the challenges of the technique are manifold. For a start, the oxidation process is irreversible, yet gradual, so the artisan must judge the change in colour accurately and stop firing the dial the moment the exact shade of blue/brown that she needs is achieved, lest the dial is “overheated” and acquires the wrong hue. Compounding this is the way subsequent applications of heat still affect the masked portions of the dial, however subtly, which must be anticipated by the artisan. The technique also demands cleanliness, as microscopic specks of dust will mask the dial and cause imperfections to surface during heating. Finally, to further complicate things, consider the size of the canvas that the artisan has to work with – a deft touch and an eye for micro details are basic requirements, to say the least.
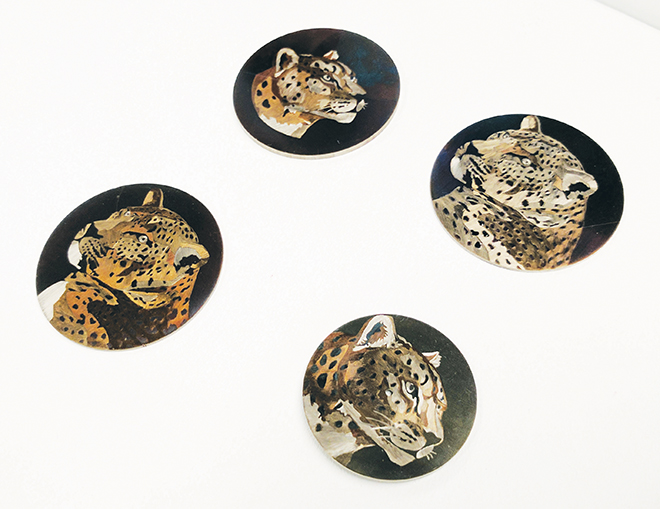
Several designs for the panther motif were considered for the first watch to feature the flamed gold technique
Cartier Métiers d’Art – Bead matching
Enamel granulation is also a technique developed by Cartier, and combines gold granulation with enamelling. Granulation is a technique first made famous by Etruscans around 3,000 years ago, and involves decorating an object by paving it with tiny granules of precious metal, usually gold, to create a textured surface. Cartier debuted this technique in its timepieces in 2013, when it released the Rotonde de Cartier Panthere Granulation, which had a panther’s head rendered with the technique using 22K yellow gold.
Enamelling is a technique that requires no introduction, but Cartier’s mastery of this technique bears mentioning. Essentially, enamelling involves working with coloured glass powders in paint form, before firing the product at various temperatures to either set the enamel or vitrify it. Commonly seen enamelling techniques are champlevé, where cells are carved from the dial and filled with enamel, and cloisonné, where cells are formed by soldering wires onto the dial. Cartier’s expertise with enamelling extends to far more esoteric variants such as plique-à-jour, which uses hollow cells without a “base”, and grisaille, which is an extremely challenging technique of painting white enamel on a black enamel base.
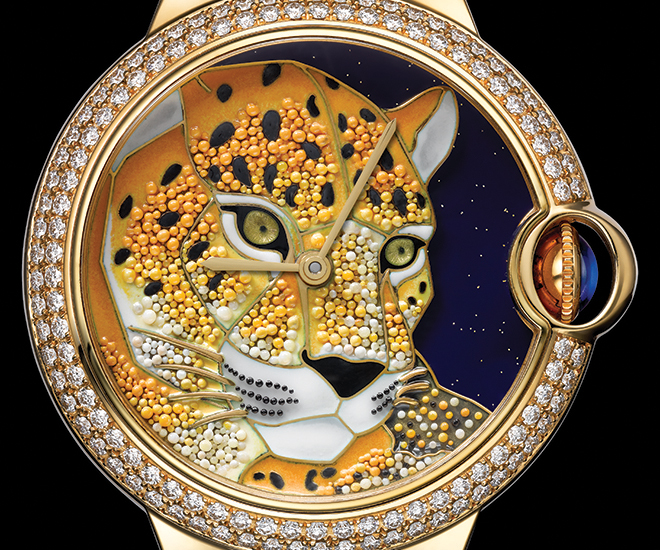
The Rotonde de Cartier Panthere Granulation uses gold granulation to create the motif of a panther’s head on its dial
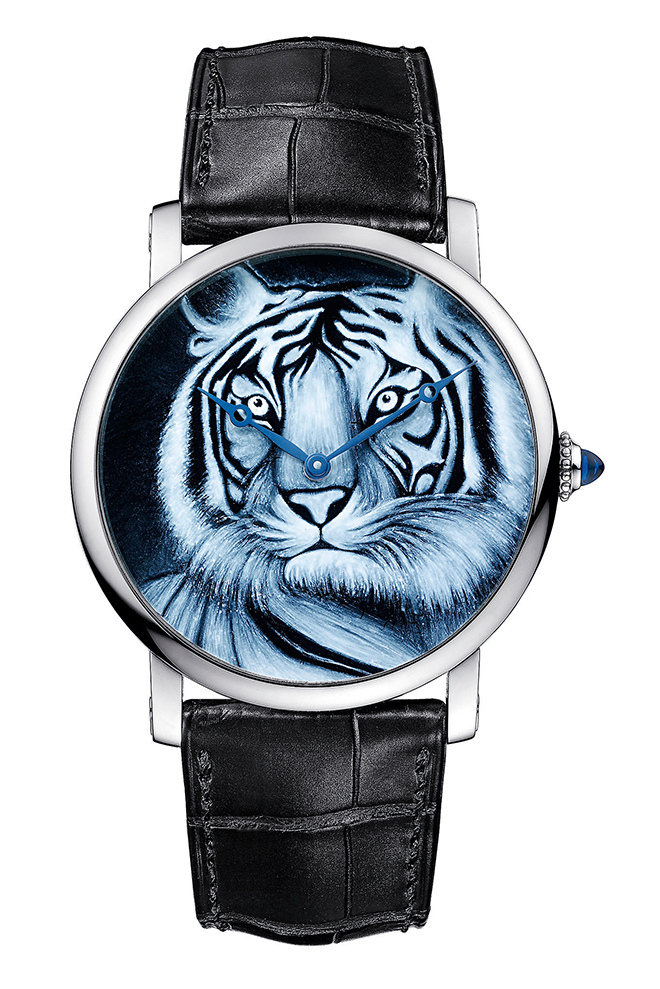
This Rotonde de Cartier watch’s tiger motif uses grisaille enamel, an extremely challenging technique that’s capable of creating highly nuanced details
Combining the two results in enamel granulation, which requires two distinct stages of production. Enamel is first drawn into threads, before tiny sections of it are broken off and re-melted using a flame. The re-melting causes the enamel to coalesce into a bead, with its size dependent on the thread’s diameter and how much of it was cut off. The first part of the process is thus to create enamel beads of various colours that are then sorted by size using a series of sieves. The second part of the technique is the actual application of the beads onto the dial, which has the panther’s outline formed with wires a la the cloisonné technique. The beads and enamel filling in the cells are applied colour by colour, then fired at different temperatures to set them sequentially. The final result combines the best aspects of granulation and enamelling. On one hand, granulation produces beads of different sizes for a textured dial with three-dimensional details. On the other, enamelling is responsible for the range of colours that gold alone cannot achieve.
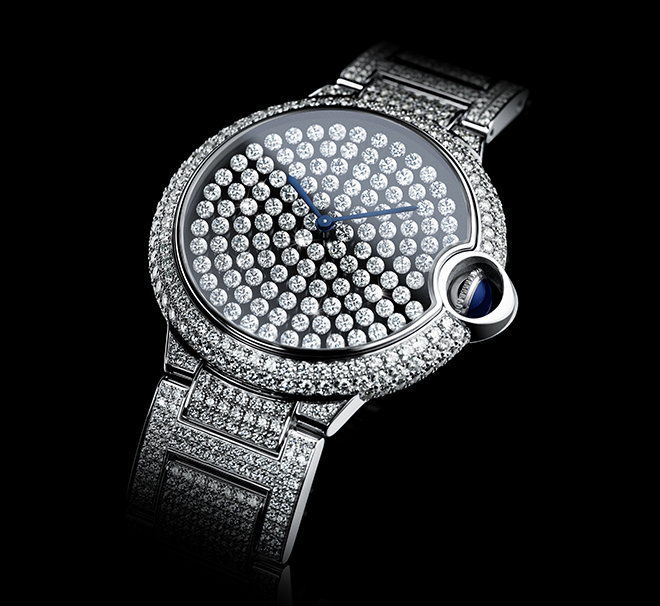
The Ballon Bleu De Cartier Vibrating Setting watch
Cartier Métiers d’Art – Set in motion
Dubbed “the jeweller of kings and the king of jewellers” by Edward VII of England, Cartier Métiers d’Art has 170 years of heritage in making jewellery and jewelled watches. The production of jewellery and jewelled watches is actually split between the brand’s workshop in Paris and the Maison des Métiers d’Art in La Chaux-de-Fond for capacity reasons, with projects completely assigned to either facility. In contrast to the computer-aided design workflow that characterises watch and movement development at Cartier, jewellery – especially high jewellery – is still produced in the most traditional way possible, beginning with two-dimensional sketches. Following this, wax models are carved and analysed before undergoing refinements to arrive at the final design, which then enters production.
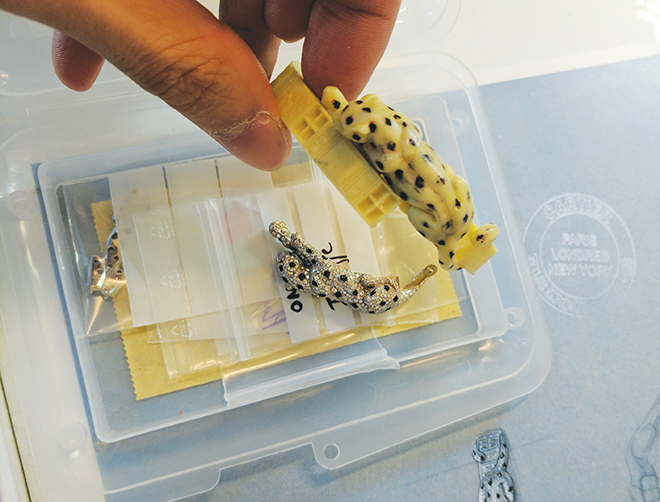
A wax mock-up of a jewellery piece, with the half finished product below it
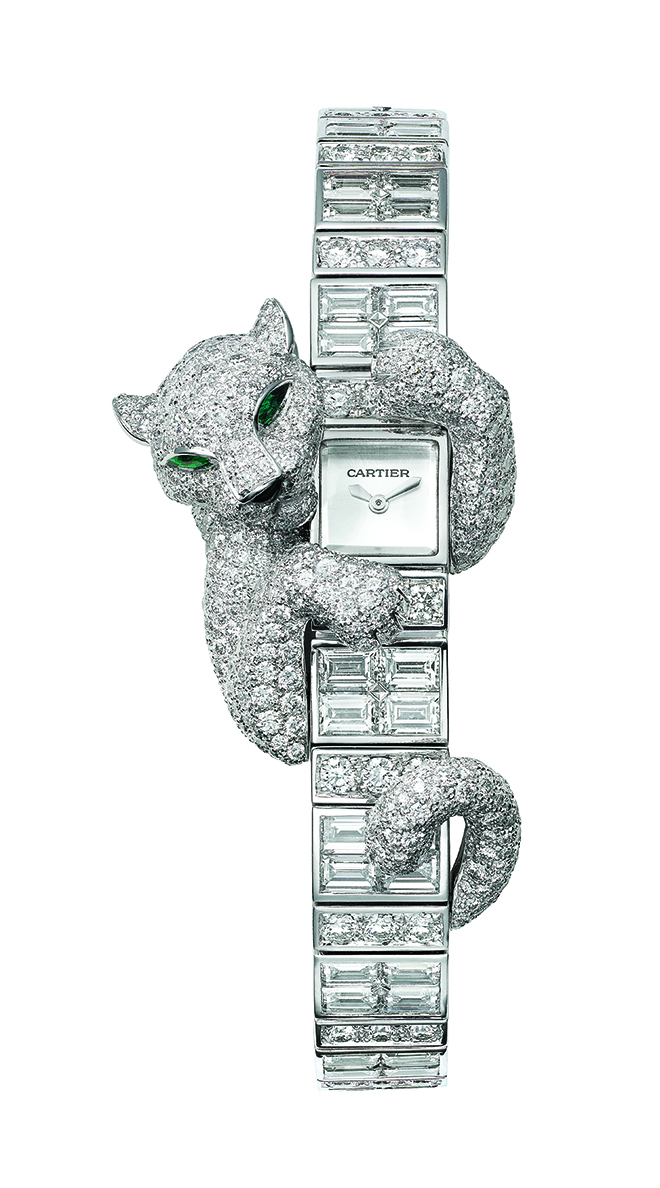
The Baguette Panthère watch uses the invisible setting, snow setting, and bezel setting techniques
Cartier’s jewellery-making ability isn’t impressive simply because of its capability to do things in-house, but also due to the sheer breadth of setting techniques it uses – and has developed. The maison has a variety of gem-setting styles at its disposal, from the common bezel setting and claw (or prong) setting, to more exotic ones like cutdown pave setting and random (or snow) setting. The exact style used depends on the required aesthetics, as well as the size of the gem to be set – snow setting, for instance, doesn’t just require stones of different sizes, but also works best with smaller stones, while cutdown pave setting is better suited for larger stones due to the difference in the perceived size of the stone vis-à-vis the metal prongs holding it in place.
Gems needn’t be static when set, though, as Cartier showed in 2015 when it unveiled vibrating setting in the Ballon Bleu De Cartier Vibrating Setting watch. Inspired by the trembling setting the maison introduced in the late 19th century, vibrating setting is used here to affix the diamonds to the dial, and took five years of research to develop. The mechanical structure used is as yet unrevealed, but this setting style is invisible and allows each diamond, which measures 0.3 carats, to move to some degree, as if it were affixed to a spring. The result is a “floating layer” of diamonds that are set in motion with the slightest disturbance to the watch, which causes them to shimmer unlike any fixed setting. To further accentuate this effect, Cartier gave the white gold dial an NAC treatment to render it black, which makes the reflections from the diamond seem even brighter.
Cartier’s in-house metiers d’art expertise has allowed the maison to develop new artisanal techniques like the ones described. What’s perhaps even more exciting, is to see how they are refined and improved upon in subsequent iterations.